Fikst Product Development
Fikst is a product development consulting firm that works with various clients in a range of industries, specializing in biomedical devices. Throughout my co-op at Fikst I did work for 3 different clients, attending and occasionally presenting at weekly meetings. My role varied by the day and the project, so I was able to gain experience in a range of skills including: mechanical design, experimental design and analysis, software and control, as well as manufacture and assembly. Below I describe a few of the major projects and tasks I completed while on co-op.
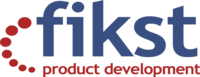
LVDT Fixture
The largest project I was tasked with on co-op was designing a measurement fixture for injection molded parts. The fixture's requirements were to measure features on high precision molded cartridges down to a single micron, while also determining the curvature of the cartridge - which was often on the order of 30 microns. This fixture was to serve as a standard measurement method for the client, the molder, and Fikst. The measurements will be used to identify errors in the molding process at the source, and also provide quality control assessment. The fixture was designed to be easy and fast to operate, in contrast to the measurement method it was replacing which took a skilled operator over half an hour per cartridge and could only be performed by the client.
I began working on this project in the proof of concept phase, constructing a simple fixture out of aluminum extrusions and spare linear stages. We successfully used the prototype fixture to sell the client on our method of using LVDT (Linear Variable Differential Transformer) contact sensors was a viable method of measuring the optical acrylic parts to the desired tolerances. From this point on I owned the design, manufacture and testing of the fixture.
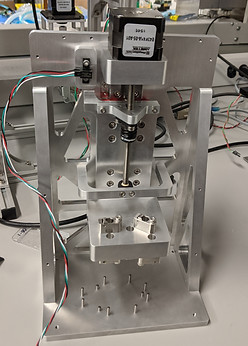
Assembled Fixture Frame
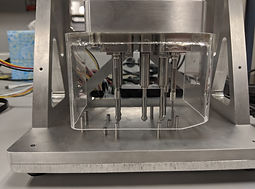
LVDT Sensors and Part Placement Area
Throughout the remainder of my co-op I developed the measurement methods and continued refining the fixture. First, I automated the stage motion using Python and a stepper motor driver, while also reading the serial input from the LVDT sensors such that the data processing could be automated in Python. Once I had developed cartridge retention methods and the repeatably of the measurements were approximately 10 microns - close to the error in the prototype fixture - I began designing a purpose build fixture in SolidWorks. The fixture was design to be extremely rigid and compact, to improve the repeatably of the measurements and reduce the overall cost of the device. I also specced various COTS parts including a NUC computer and a stepper motor driver. The custom machined aluminum parts were ordered from a manufacturer in China.

Initial Proof of Concept Fixture

Fixture as Shipped to Client
When the parts arrived, I assembled the fixture and began testing. The preliminary testing results exceeded expectations and the fixture's repeatably was measured to be less than 1 micron. Prior to shipping the fixture to the client I developed a Python UI, which would allow for the operation of the fixture and would also guide the user through the measurement procedure. The interface showed plots of the measurements, in addition to numerical readout, so the operator could observe and analyze the measurements in real time. I shipped the first fixture to the client in my last week of co-op, and Fikst has since begun work on building a second version of the fixture.

Python UI for Fixture Operator

Die Cutting Block with Insert Installed
Die Cutting Insert
The first project I took through the full design process was designing an insert to extend the life of a jig for die cutting the foil on the top of heat sealed bottles. The client came to us with the problem that their aluminum jig used to hold the bottles while they were being die cut was being marred and cut by the blades of their die cutter. They wanted to have something to extend the life of the relatively expensive aluminum jig. A short brainstorm led to the leading idea of creating a consumable insert out of HDPE which was easy and inexpensive to manufacture that sat in a recess within a machined aluminum jig to hold the bottles. I modeled the design in SolidWorks and did the CAM using the HSM Works plugin. Then I machined the aluminum block and the HDPE insert on our in house CNC mills. The client really liked the new design and ordered an additional 60 inserts for use when the initial shipment of 8 wore out.
Foil Cold Forming
One of the more interesting projects I was tasked with on co-op at Fikst was determining the maximum formable draft angle and depth for an aluminum foil. One of our clients wanted to redesign their packaging from the existing pouches it was stored in to a tray with a heat sealed lid. They received models from an industrial designer, then tasked us with trying to replicate the industrial design but with an aluminum foil. The foil was required instead of a typical vacuum formed foil because the packaging could not be vapor permeable.
I started the design process by designing a custom positive insert for the cold forming machine Fikst had, then parametrically surface modeling the resulting shape of the foil. The parametric model created in SolidWorks was able to display the resulting shape of the foil based on the constraints of the foil sealer. Using the model, I created a matrix of depths and draft angles to test. From the test matrix I had a set of designs for the negative portion of the mold (a plate to define the outer edge and fillet radius of the formed foil), which I machined out of aluminum.
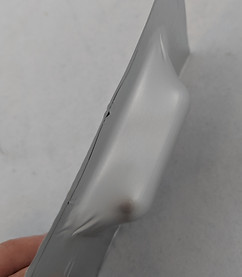
Sealed Cold Formed Package
I performed the matrix of tests with multiple trials of each depth and draft angle. I then summarized my results and presented them to the client. I reran some of the most promising results, then heat sealed the top on the package and shipped the fully packaged tray to the client. Unfortunately the foil tray was not rigid enough and the package opening experience was less than satisfactory. The approach of designing a cold formed aluminum tray was dropped, however I gained valuable experience in experimental design in a field of study I would not have normally been exposed to.
Holiday Puzzle
Every year, Fikst designs and manufactures a holiday puzzle for their clients. This year's puzzle was a multi-stage ball maze with a rotating half. When the maze was completed a latching mechanism in the cap would open a door to reveal candy stored within the puzzle. I worked on the team tasked with designing the cap assembly and the door latching mechanism. I was also involved heavily in the manufacture and assembly of the 100+ puzzles constructed for clients and employees.

Assembled Holiday Puzzle